Machine faults are not always caused by the machine
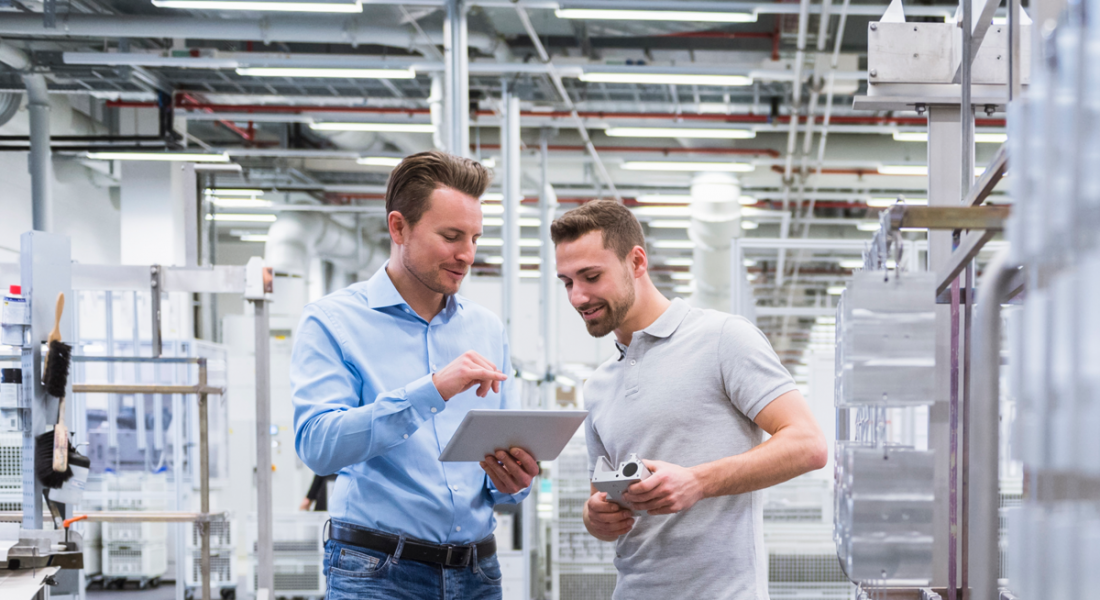
Time and again, the injection molding machine of a plastics processing company breaks down completely unexpectedly. This can have many causes. More and more frequently, it is due to poor voltage and power quality - as was the case here. Rolf Wagner, Head of Sales at econ solutions, explains how this was identified and rectified.
After the machine breakdowns, the technician checked the machine and all the controls several times, but could not find anything wrong. Rather by chance, the production manager then discovered anomalies in the voltage quality when he evaluated the recordings for the operational energy management. This revealed an unusually high harmonic content in the production area, which could be responsible for the machine failure. This is because harmonics are superimposed on the voltage and current fundamental oscillation and thus change the sinusoidal voltage. This can lead to problems such as machine failures or malfunctions, IT crashes, unexpected tripping of fuses and circuit breakers or even damage to power capacitors and compensation systems.
After the next machine failure, the production manager immediately checked the recordings and was again able to identify a high harmonic content. A connection was therefore obvious. The plastics processor called in econ solutions to check this and take appropriate measures. The company was already using the energy management system that had provided the indication of the poor voltage quality.
Measurements lead to the cause
In order to check what was causing the harmonics - and whether they were caused by the company itself or fed in by the energy supplier - the experts from econ solutions carried out detailed measurements of the voltage at various points. The most important measuring points in such cases are generally after the transformer feeds on the low-voltage side, directly at the affected machines and at large consumers such as converters or rectifiers. As the faults usually occur unpredictably, as in this case, it is advisable to measure the voltage continuously. The econ sens3 energy and power measuring device is ideal for this, as it can be installed quickly and without interruption and records all important characteristics of electrical power, energy, currents and voltages. The plastics processor also already uses econ's energy management software, so that the measurement data from the sens3 is automatically transmitted via the company network (TCP/IP) and integrated into the software. It offers even more and even simpler evaluation options.
The measurements showed that the high harmonic content was caused by the company itself. It was caused by the use of several non-linear consumers and power electronics, including rectifiers, motor speed controls, the uninterruptible power supply and the recently installed LED lighting in the production hall. They all have a non-linear current consumption, which is responsible for the harmonics. These overlap the voltage and current fundamental oscillation, which in turn affects the sinusoidal voltage and ultimately led to the failure of the injection molding machine.
Decreasing power quality
The use of such non-linear loads has generally increased, and electricity is increasingly being distributed via HVDC lines (high-voltage direct current transmission). As a result, it is becoming increasingly common for energy suppliers to deliver inadequate grid quality. This is defined in EN 50160.
Definition of power quality: EN 50160
EN 50160 defines the power quality, i.e. the voltage characteristics with which energy suppliers must feed energy into the public low- and medium-voltage grids. To this end, the standard specifies limit values for all key characteristics of the grid voltage at the grid connection point, such as frequency, harmonics, fast and slow voltage changes, flicker, unbalance and transients. The limit values from the standard are already stored in the econ sens3. However, they can also be set individually, as even minor deviations can have negative consequences - depending on how high the grid impedance is in the company. If the limit value is exceeded, the measuring device either triggers a potential-free contact or sends an e-mail with the type of fault in plain text and a graph of the current and voltage curve at the time of the fault to predefined e-mail addresses. It also stores the waveform of the current and voltage in the internal memory. Limit violations and grid events such as harmonics, voltage fluctuations, flicker, etc. are clearly displayed in an EN 50160 report. The report is available in txt format and as a JSON export, so that the event can also be traced retrospectively and, if necessary, proven to the energy supplier. In this case, however, the cause lay within the company. The first step was to remedy the situation by disconnecting all consumers from the injection molding machine's power supply as far as possible or disconnecting their control systems.
Active filter compensates for harmonics
In order to permanently reduce the harmonic components, econ solutions designed an active harmonic filter and connected it in parallel to the harmonic generators. It neutralizes their harmonic currents at the connection point by analysing them and supplying the counter-phase compensation current. This means that the combination of harmonic filter and load in the grid behaves like a linear load that consumes a sinusoidal current. One variant is a passive filter. It consists of a tuned absorption circuit for each harmonic, which is made up of inductances and capacitances. However, the passive filter is more difficult to implement in practice and is only ever designed for the respective installation. If this is changed or extended, the filter may also need to be adapted, which requires new investment. For these reasons, econ solutions chose the active harmonic filter here. This enabled all consumers to be reconnected to the grid and the injection molding machine has been running completely reliably ever since.