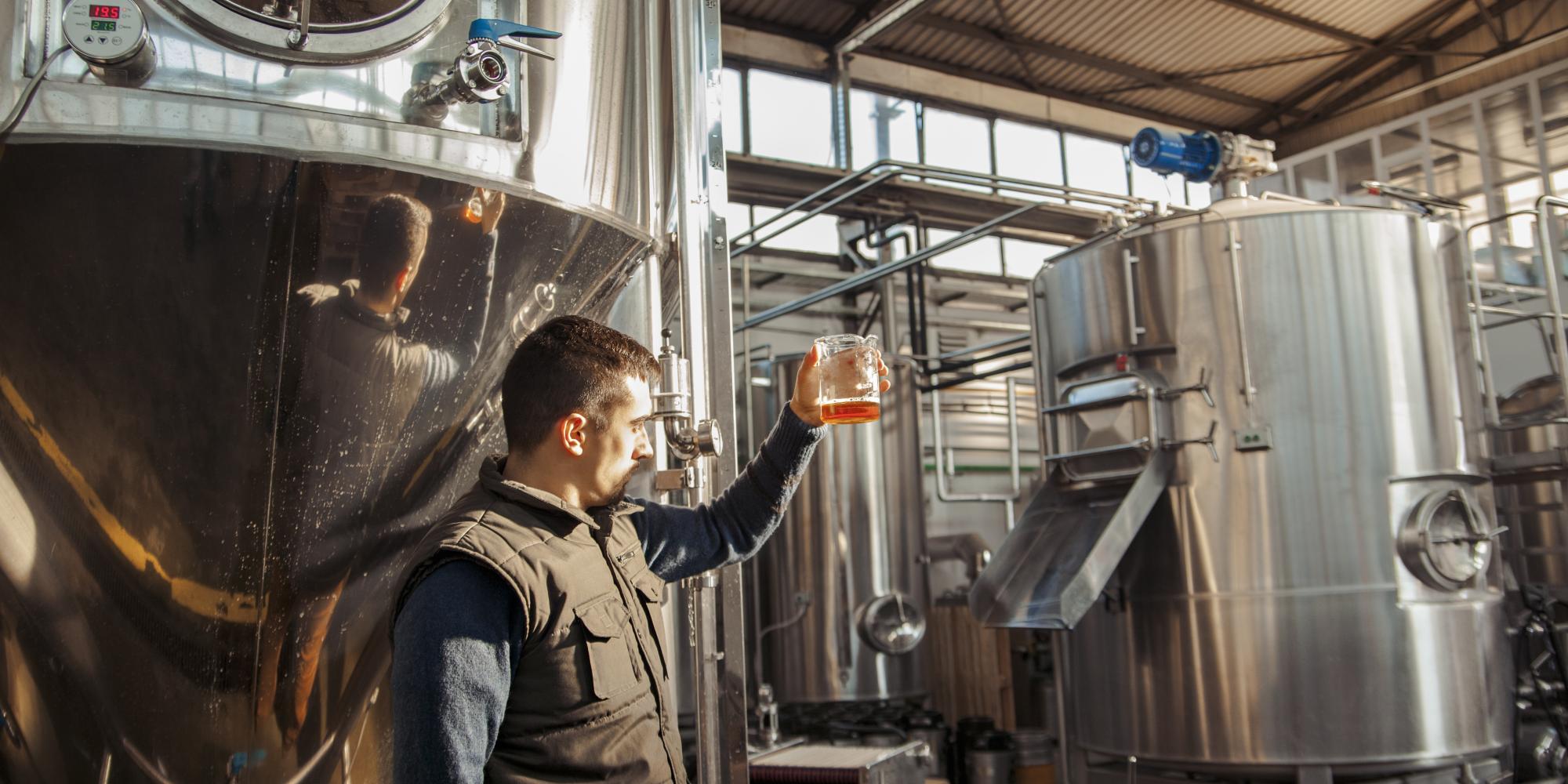
Alpirsbacher Klosterbräu
Also keeping an eye on water consumption
For many manufacturing companies, electricity consumption is the main focus. For Alpirsbacher Klosterbräu, water is at least as important as the most expensive medium. With our energy management system, the brewery is also ensuring greater efficiency here.
Alpirsbacher started with energy management by reading meters manually and evaluating them with the help of Excel - as is the case with many companies. However, the disadvantages of this approach soon became apparent: The time required is high and the limited evaluation options provide little basis for identifying optimization potential.
With an energy management system, the process was to be digitalized and thus largely automated. Alpirsbacher also wanted more detailed evaluations. Berthold Bader, Head of Project Management and Operating Technology at Alpirsbacher Klosterbräu, describes another requirement: "We had all kinds of meters in use, from impulse water meters to electricity meters with an Ethernet interface, as well as the compressed air system with a Modbus output. We therefore needed a system into which we could integrate all our meters. We found that with econ. In the meantime, we have not only integrated the hardware into econ, but also data from our 'Braumat' process control system. The new ERP system, which we are currently putting into operation, will follow."
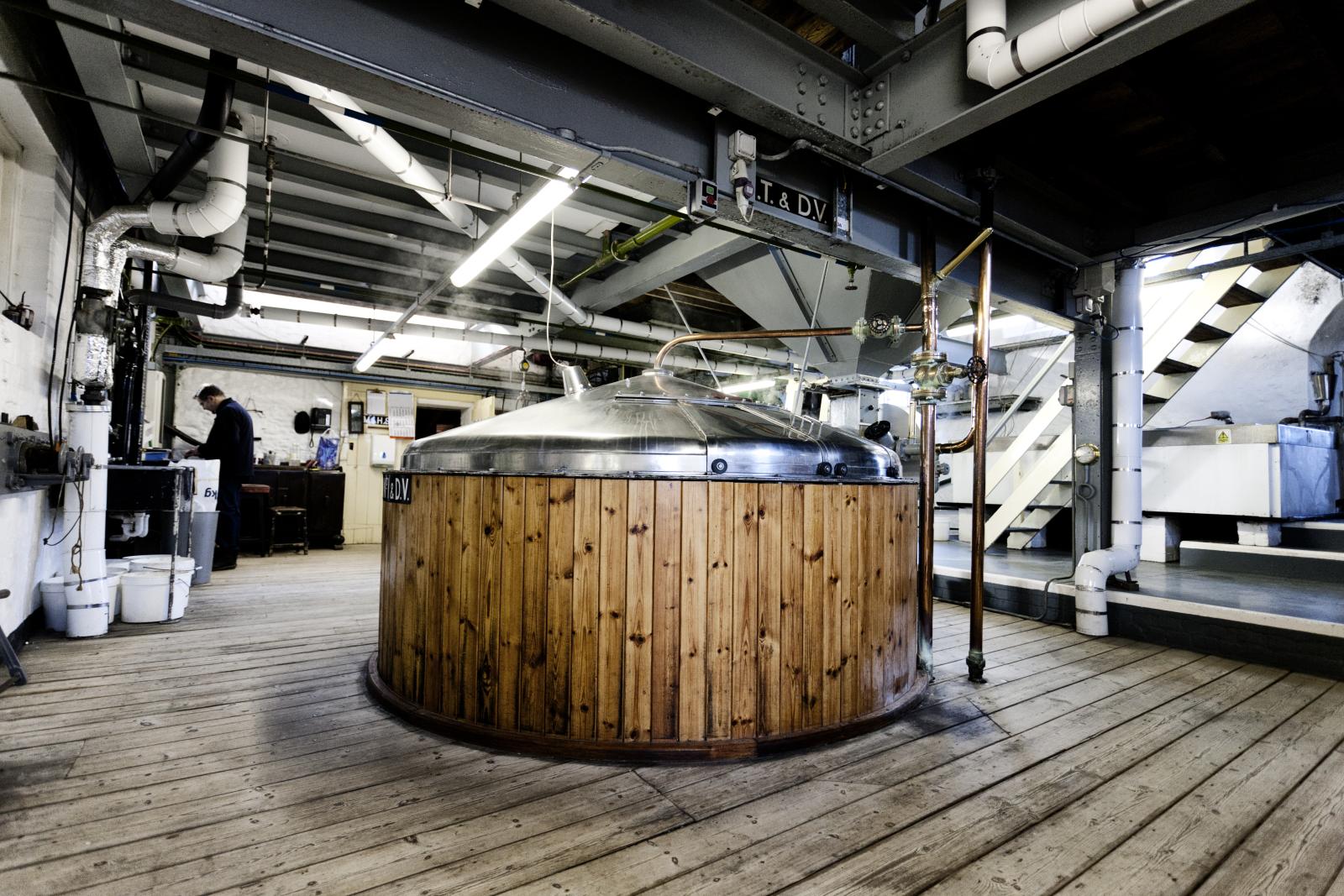
Key figures through integration of the ERP and process control system
This is because the ERP system provides the bottled beer quantities almost in real time. Together with the measurement data from the meters, the econ4 software continuously calculates the energy performance indicators (EnPI) for bottling. These are primarily the electricity and water consumption per hectoliter of beer filled. "Perhaps transferring data the other way round - i.e. from econ to the ERP system - will also be interesting, for example for billing energy quantities," says Berthold Bader.
The meter data from production first flows into the Braumat process control system so that, for example, the cleaning system switches to the next step after a certain amount of water has been used. The data from Braumat flows into econ4 to record and evaluate - in this case - the amount of water used in the cleaning system.
The connection between Braumat and econ4 is important in order to be able to determine the key figures for production. This means that Alpirsbacher always knows how much heat, electricity, water, compressed air andCO2 it consumes per hectoliter of beer or mixed beer beverage. As far as possible, these key figures are considered on a department-specific basis for the brewhouse, the fermentation and storage cellar and filtration. If significant fluctuations occur here, it is clear that the cause does not lie in the production process, but that other influencing factors play a role. It is then worth looking for the causes.
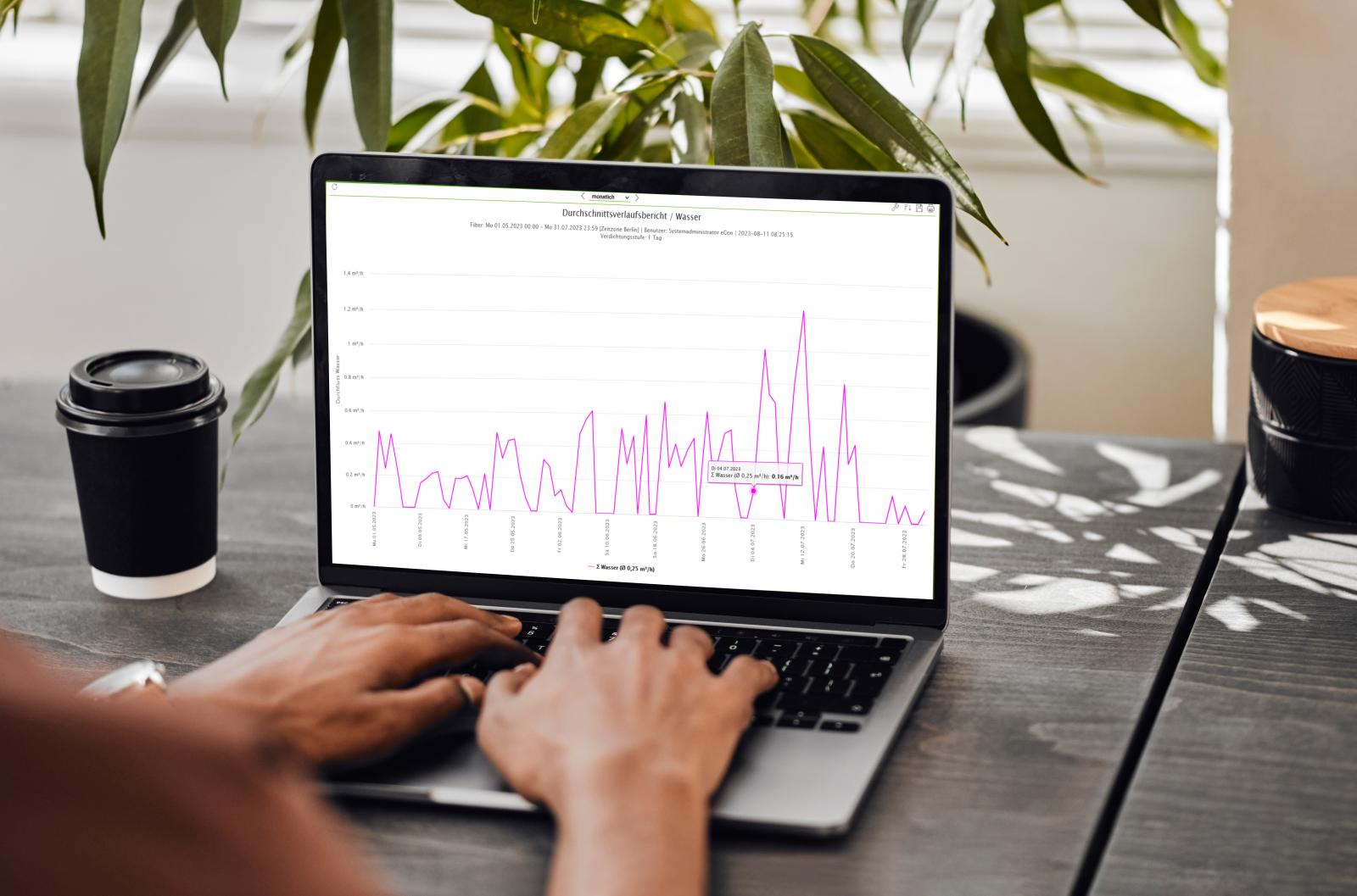
Preventing water wastage, increasing operational safety
"This applies above all to water - our most expensive medium due to the high water and wastewater prices," explains Berthold Bader. In addition to the general reduction in water consumption, the focus is therefore on leak detection. To this end, Berthold Bader has set threshold values for water consumption within 24 hours. If one of these values is exceeded, he receives a notification from the system.
"This has already saved us from a critical situation. There was quite a large leak in the underground water pipe between the two Alpirsbacher plants - on a Friday, of course. It was only thanks to the notification from econ4 that we knew immediately and were able to do something about it straight away. Otherwise our elevated tank would have run empty over the weekend and we wouldn't have been able to produce on the following Monday," reports Berthold Bader.
The situation was similar with the bottle washing machine: here, increased water consumption was quickly traced back to a defective valve. Without the measurement data and evaluations in near real time, the increased consumption might have gone unnoticed for weeks.
Harnessing unsuspected efficiency potential
The refrigeration system is the largest consumer of electricity. Among other things, it cools a tank farm whose insulation is not state of the art due to its age. It was therefore clear that its electricity consumption was somewhat dependent on the outside temperature. "But we were surprised that the specific consumption was so much higher in summer. Of course, we took the higher production volumes during this time into account," says Berthold Bader. That is why we are now considering improving the insulation of the tank farm in order to reduce its electricity consumption.
This was also the reason for purchasing a new filling line. "It is very helpful to have good data, especially when making such large investments. This means we know the savings potential quite precisely and can carry out realistic profitability calculations," explains Berthold Bader.
A surprising efficiency potential was also revealed in the compressed air generation: Although the system was only ten years old, it had poor specific values on closer inspection in econ4. Alpirsbacher has therefore now replaced it with a new system and reduced electricity consumption for compressed air by 40 percent. The new compressed air system will pay for itself within four years.
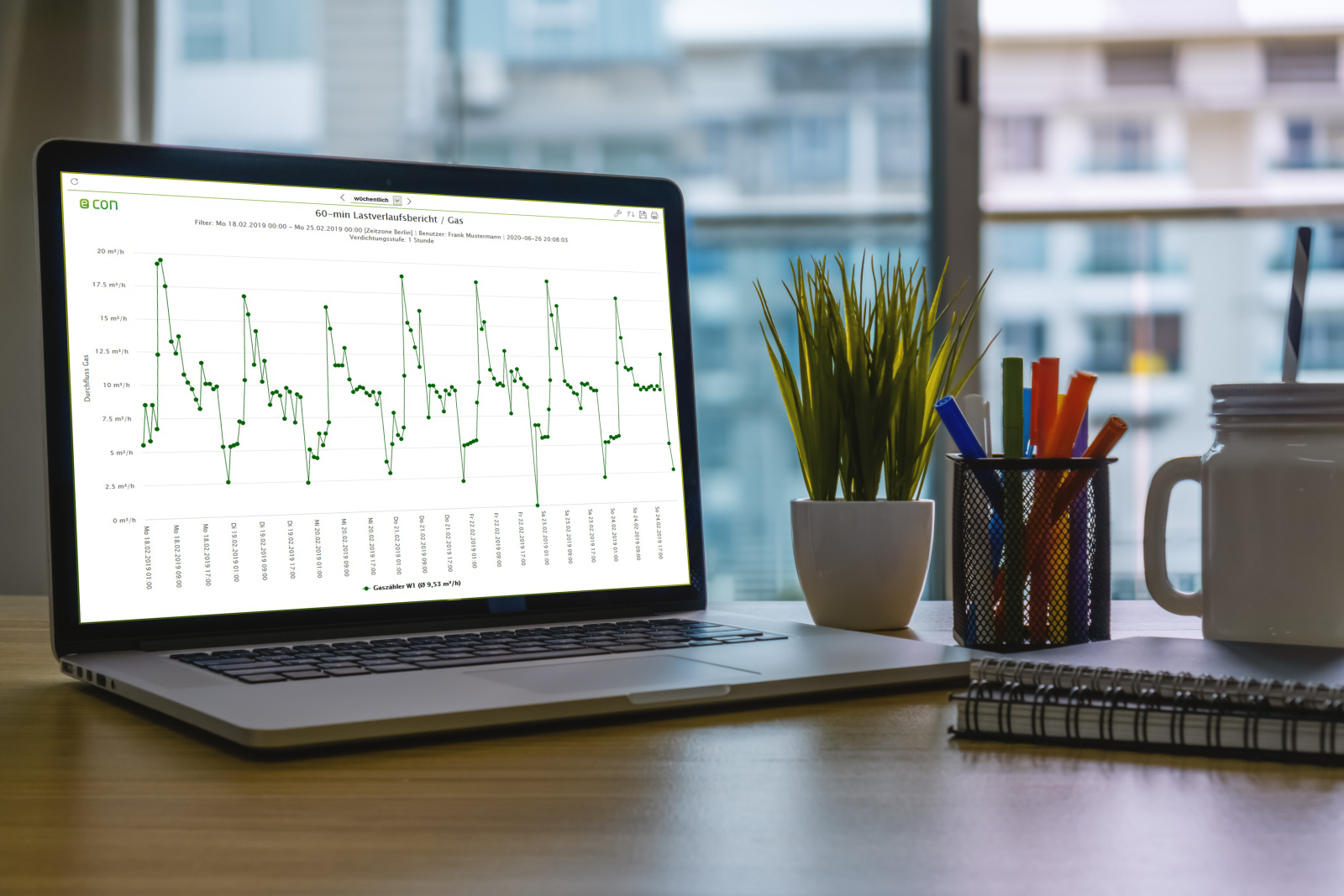
Electricity peaks reduced
With the energy management system, Alpirsbacher has also introduced peak and charging load management to counter rising grid usage fees.
In 2021, the brewery installed the first charging stations for e-vehicles on the company premises. This prompted the company to switch to the new econ peak version of load management. In the event of an impending peak load, it automatically switches off or reduces consumers that are not necessarily needed.
Alpirsbacher now has ten charging points of 11 KW each, all of which are connected to econ peak, as well as around ten consumers from production. "And more are gradually being added. This is because smaller consumers also have a relevant effect on the system in order to avoid peak loads as far as possible," says Bader.
Alpirsbacher has even been able to reduce its peak loads somewhat, even though new consumers have been added and the production volume has increased by around 30 percent over the last ten years. "Not only the power peaks, but also our electricity and gas consumption have remained at almost the same level despite a significant increase in production," reports Berthold Bader.
Alpirsbacher is already in the process of expanding the econ system with additional sub-meters in order to be able to record and evaluate all media in depth. The aim is to allocate consumption to the individual cost centers as far as possible.
"Looking back, I would digitize as many meters as possible as soon as the energy management software was introduced," says Berthold Bader. "But we are now gradually catching up. I am very satisfied with econ, our expectations regarding the interfaces have been fully met, and the software also provides a wide range of attractive, informative reports. I would choose econ again today."
As an SME, Alpirsbacher Klosterbräu is 16427-certified. Today, however, we have such good data from econ that we would certainly get ISO 50001 certification from a standing start.
Berthold Bader, Head of Technology and Quality Management at Alpirsbacher Klosterbräu