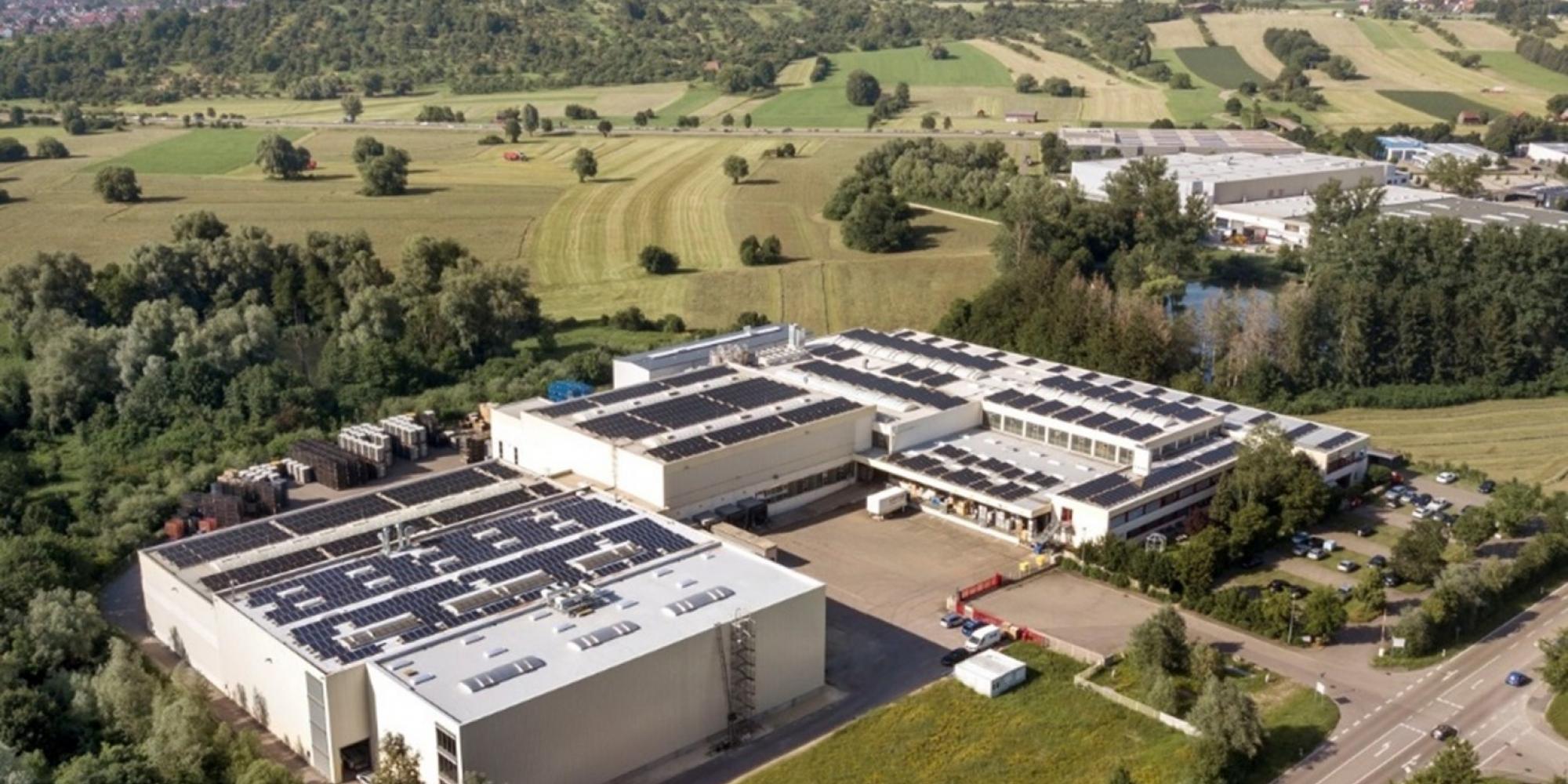
Fried Kunststofftechnik
From energy data acquisition to comprehensive analysis
Fried Kunststofftechnik is one of our long-standing customers: The specialist for customer-specific plastic solutions has been using the econ energy management system for around ten years. Since then, it has continuously expanded and refined the measuring system. And Fried has taken the next step: Energy data acquisition now forms the basis for deepening the understanding of energy-related processes in the company and thus further optimizing the energy system, increasing energy efficiency and reducing CO2 emissions.
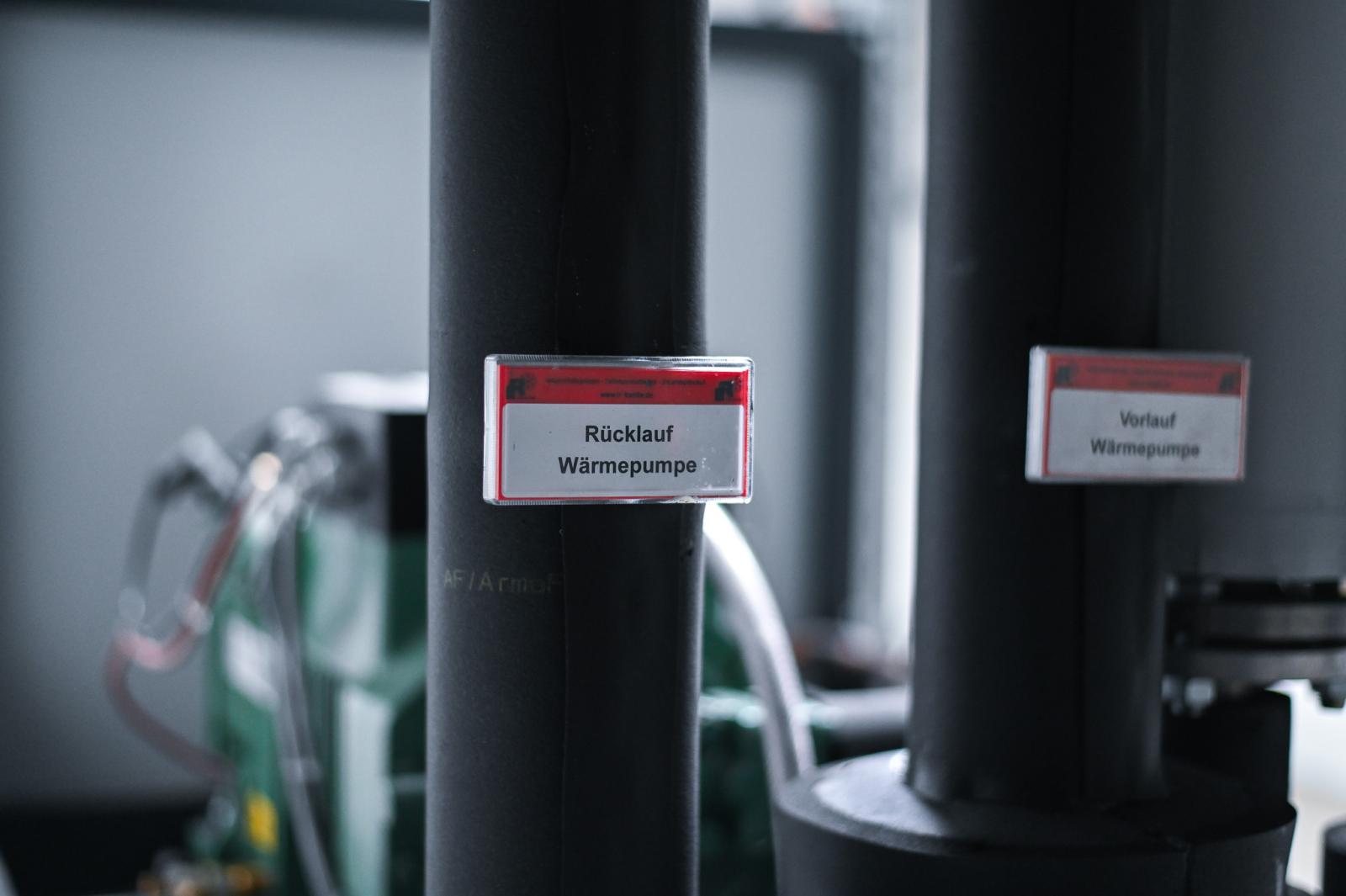
Automated calculation of key figures
Initially, electricity was the biggest cost factor in the energy sector, but today the focus has shifted to a holistic view of electricity, gas and heat. Fried primarily uses natural gas to generate heat. To reduce consumption here, Fried now uses a heat pump. It uses the waste heat from the machines to generate process heat for the drying oven. A heat buffer storage tank is connected between the heating system and heat pump on one side and the drying oven on the other. In cases where the heat pump is not running, e.g. for maintenance reasons or because no waste heat is available from production, the heating system can supply the process heat.
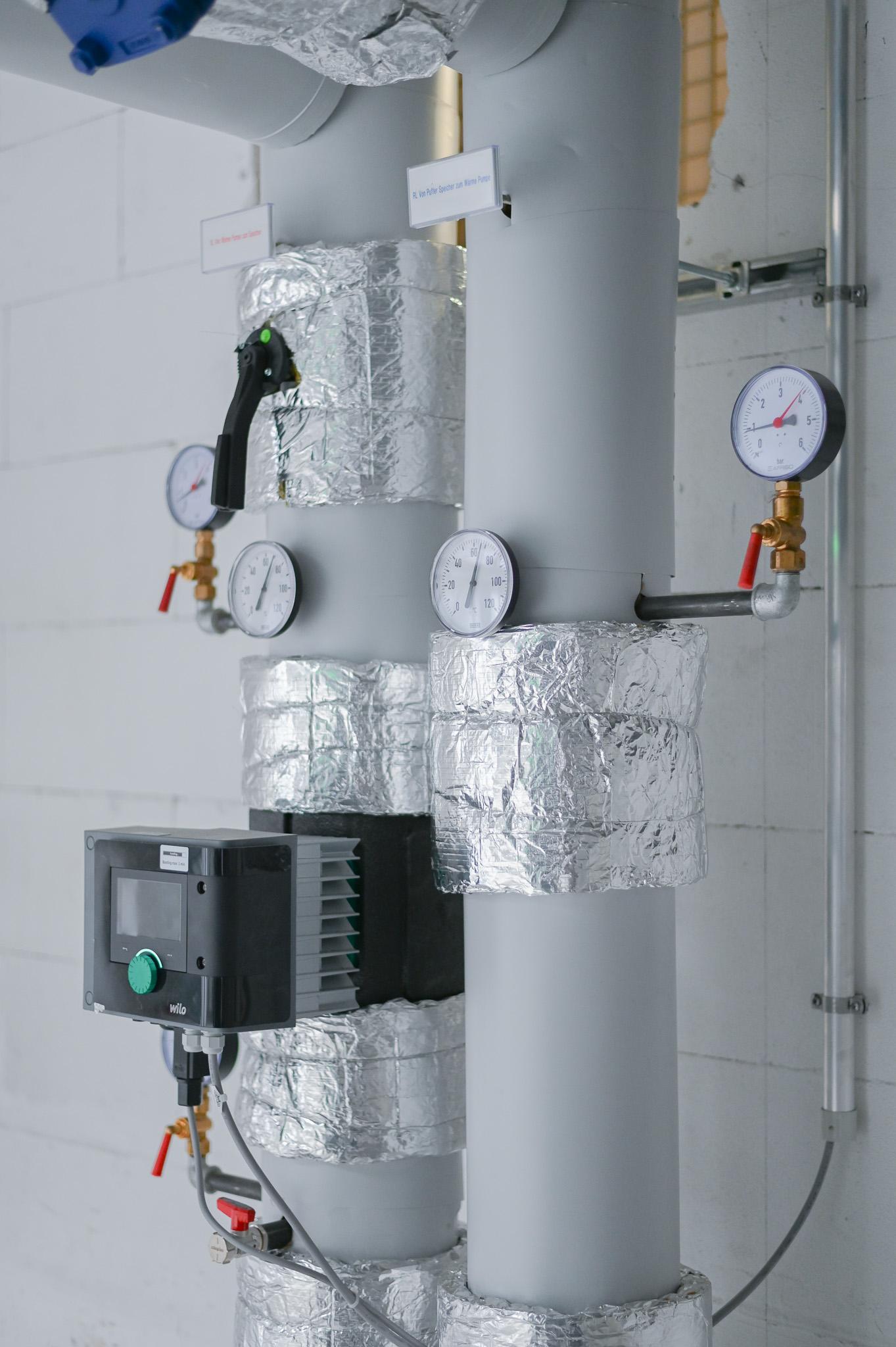
A heat meter on the drying oven measures the heat energy required and is connected to the econ system via the econ connect interface solution. However, it is not possible to distinguish whether the heat comes from the heat pump or the gas heating system. However, it was the aim of Dr. Andreas Tewald, Energy Management Officer and Head of Work Preparation and Facility Management at Fried, to be able to quantify the gas savings potential of the heat pump.
"These results can then be communicated to the management as well as to partners and funding providers," says Dr. Tewald. "For tasks like these, we are glad that we can use econ not only as a measurement system, but also to determine key figures." To this end, Dr. Tewald has stored a formula in econ that the system uses to automatically output the gas consumption of the drying oven. "With these concrete values, we can make completely different statements and forecasts than with pure estimates." In addition, the energy management officer also determines the actual efficiency of the heat pump. This means he does not have to rely on the manufacturer's specifications.
In addition to the gas savings, the additional electricity requirement must also be taken into account when calculating the cost-effectiveness of the heat pump. Dr. Tewald has stored the prices for gas and electricity in econ for this purpose. "It is helpful with econ that energy can be viewed not only with kWh glasses, but also with Euro glasses - even with flexible tariffs."
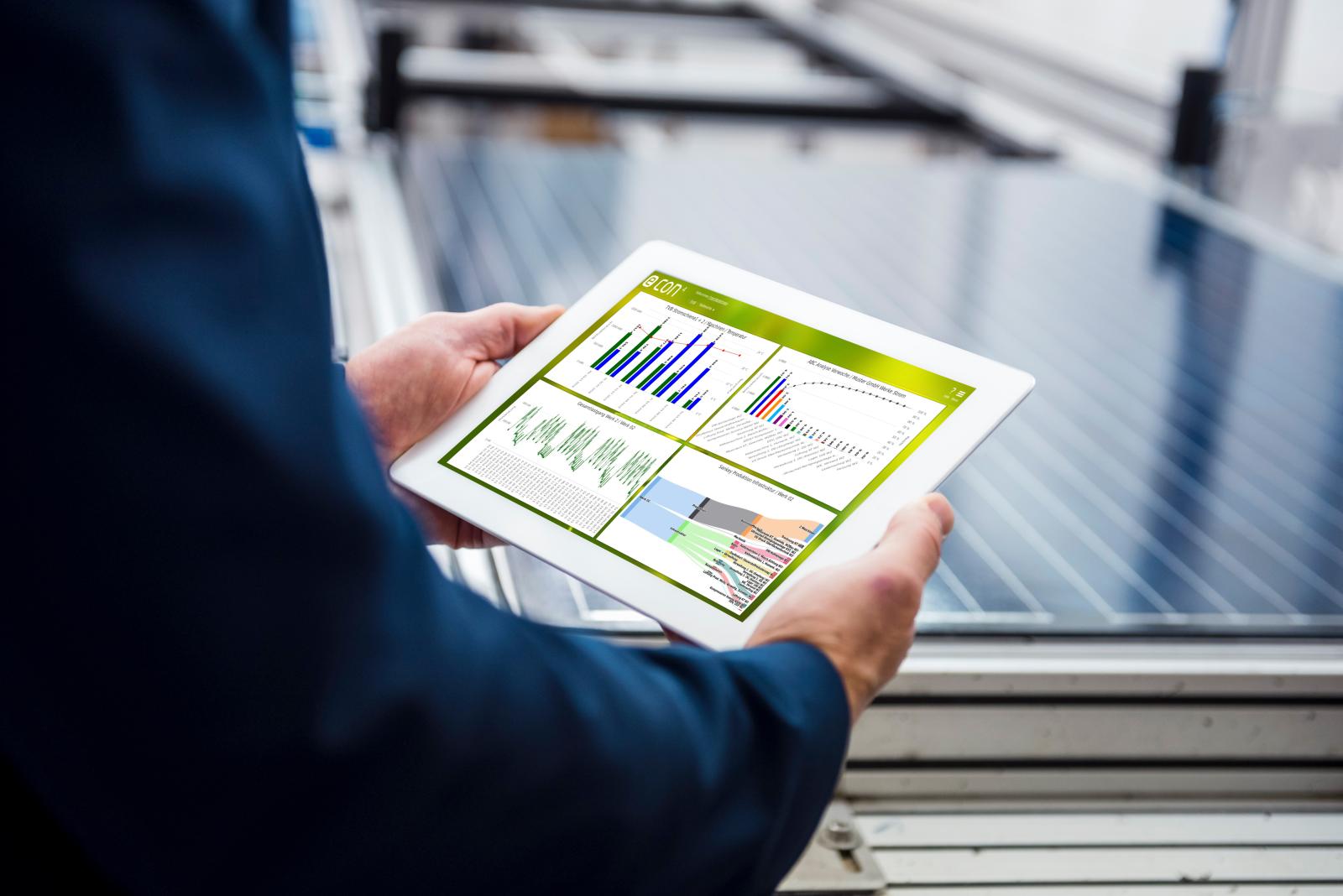
Measurement data provides information on waste heat potential
Fried usually uses new or replacement purchases to refine the measurement system and gain more detailed insights into the energy processes. When designing a new central cooling system, Fried had heat meters installed in the individual waste heat circuits to find out how much energy was being dissipated. The meters were also connected via econ connect. "This not only allows us to identify the potential for using an additional heat pump, but also to easily report data to the waste heat register," reports Dr. Tewald.
Based on the knowledge gained from the waste heat load profile and the positive experience with the first heat pump, Fried is now planning to procure another one. The data also provides a solid basis for dimensioning the system.
Expansion of the measuring system and new systems
When installing a new paint shop, Fried had additional current sensors integrated: With additional econ sens 3, the power consumption of the individual sub-processes, such as conveyor technology, robots and ventilation technology, can now be recorded separately. This enables a better energy understanding of the system and more detailed analyses of energy consumption. Increasing electricity consumption, for example, can be traced back to individual sub-processes, such as dirty filters.
"The time for filter replacement can also be determined, as usual, via the increase in pressure. However, thanks to the data from econ, we also know that it is more efficient and economical to change the filter early in order to prevent expensive, exponentially increasing electricity consumption," reports Dr. Andreas Tewald. "Such correlations only become apparent through the measurements and the reports in the software." The energy management officer has then stored corresponding limit values in econ. If these are exceeded, the person in charge receives an email informing them to change the filter.
Learning: Don't neglect the documentation
Dr. Tewald would like to pass on one experience: "It is advisable to always maintain the system documentation, especially if several people are working with the system."
When the energy management system was introduced, econ solutions took care of both the installation and the documentation. As described, Fried has successively expanded and refined the system since then. In the course of day-to-day business, it often got lost in the shuffle to keep track of the documentation. "As a result, we always have to get an overview first before we use measured values to determine key figures, which takes time," explains Dr. Tewald. For this reason, econ has now been commissioned to bring the documentation back up to date.
This will enable Fried to use the econ system even more efficiently in order to further optimize its energy use and also meet increasing requirements for energy efficiency and sustainability.
It helps us a lot that we can use the econ system not only as a measurement system, but also for the automated determination of key figures.
Dr. Andreas Tewald, Energy Management Officer and Head of Work Preparation and Facility Management at Fried Kunststofftechnik